Anand Raj
Despite the rise of other transportation options, railways remain crucial in modern times. They efficiently move bulk freight, offer eco-friendly passenger travel, stimulate economic growth, ease urban congestion, and contribute to sustainability efforts. From supporting global trade to shaping our cities, railways continue to leave an undeniable mark on the world. Railway sleepers are one of the most critical components in a rail network [1]. They are the structures that transfer the loads from the wagon wheels to the ballast, which in turn transfer the loads to the underlying strata [2]. A key role has been played by railway sleepers in maintaining the vertical and horizontal alignments of the track network. Fig.1 shows a typical cross-section of a railway track.
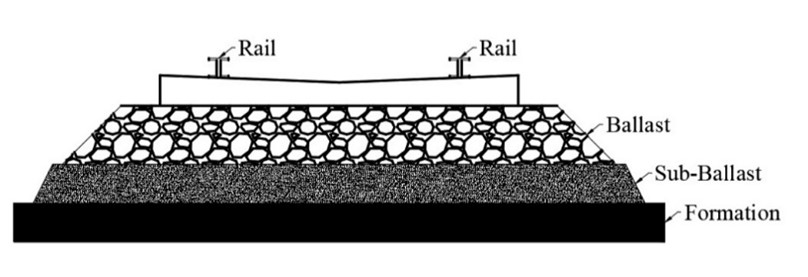
Fig.1 Cross-section of a ballasted railway track
Railway sleepers endure both static and dynamic loads. While minor impact loads occur during normal train operation, significant impact loads, which have the potential to severely compromise the structural integrity of the sleepers, occur during derailments. Typically, the damage incurred from derailments renders prestressed concrete sleepers beyond repair. Consequently, enhancing the energy absorption capability of sleepers becomes paramount. One promising approach involves incorporating worn-out tyre crumb rubber into concrete, creating rubber concrete (Rubcrete). However, this substitution often compromises strength compared to traditional concrete. To address this drawback and enhance crack control, researchers have turned to fibres. Steel fibres excel in managing larger cracks (macrocracks), while polypropylene fibres effectively regulate microcracks. Additionally, fibres can potentially boost the energy absorption capacity of concrete, paving the way for fibre-reinforced Rubcrete to withstand high impact loads.
However, before widespread adoption, rigorous testing is essential to ensure compliance with regulations like those established by India’s Research Designs and Standards Organisation (RDSO)[3]. These regulations mandate successful completion of specific tests, including:
- Rail seat static test: Evaluates the sleeper’s performance under static load at the crucial rail-sleeper interface.
- Centre top and bottom bending tests: Assesses the sleeper’s behaviour under bending forces applied at the top and bottom centre points.
- Impact tests: Estimates the impact resistance of sleepers subjected to impact loads.
Thus, comparison of the performance of various sleeper variants was carried out to assess their viability in service conditions. The following material variants were used:
- Concrete sleepers (OC): The reference sleeper.
- Rubcrete sleepers (RC): Sleepers in which 15 % volume of fine aggregates is replaced with crumb rubber.
- Polypropylene fibre reinforced concrete (PPFC) sleepers: Sleepers with 0.2 % of polypropylene fibres.
- Polypropylene fibre reinforced rubcrete (PPRR) sleepers: Sleepers with 0.2 % of polypropylene fibres and 15% crumb rubber.
- Steel fibre reinforced concrete (SFRC) sleepers: Sleepers with 0.75% of steel fibres.
- Steel fibre reinforced rubcrete (SFRR) sleepers: Sleepers with 0.75% of steel fibres and 15% of crumb rubber.
Experimental investigations were limited to scaled models to facilitate easy handling of sleepers and reduce material wastage. Fig. 2 presents the testing of scaled model of sleepers for static and bending tests. Fig. 3 shows the ultimate loads of sleeper models during static and bending tests.
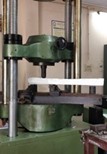
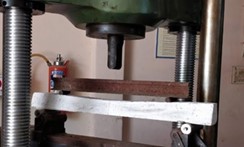
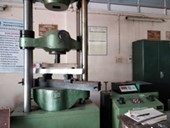
(2a) Rail seat static test on scaled sleeper models
(2b) Centre bottom bending tests on scaled sleeper models
(2c) Centre top bending tests on scaled sleeper models.
Fig.2 Testing of scaled models of sleepers for static and bending tests[4]
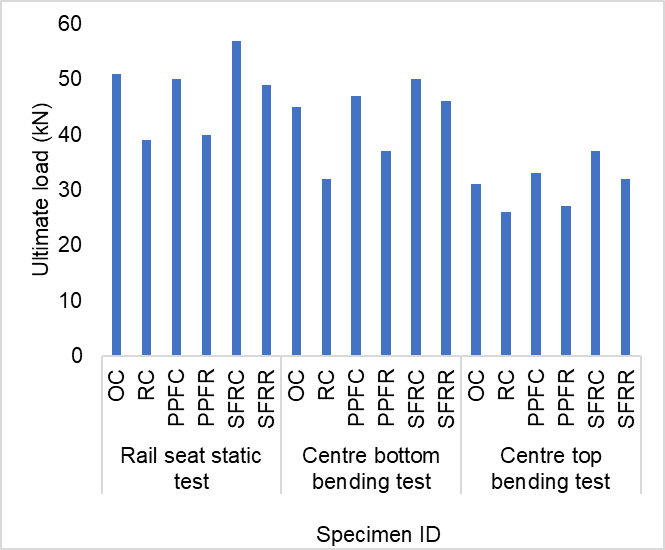
Fig.3 Ultimate loads of sleeper models during static and bending tests
The voids in rubcrete results in reduced load carrying capacity of rubcrete and fibre reinforced rubcrete sleepers. Polypropylene fibres added to concrete slightly delayed the appearance of tiny cracks. This is because the fibres helped bridge small gaps in the concrete, initially slowing down the formation of microcracks. However, once the cracks were developed, their contribution to the overall strength of the concrete became negligible. Steel fibres in concrete effectively bridged and slowed down the growth of cracks, significantly improving the overall strength of the sleepers. Even when cracks formed in these steel fibre-reinforced sleepers, the fibres held the material matrix together for longer, preventing them from breaking apart quickly. This resulted in significantly better performance compared to sleepers reinforced with polypropylene fibres.
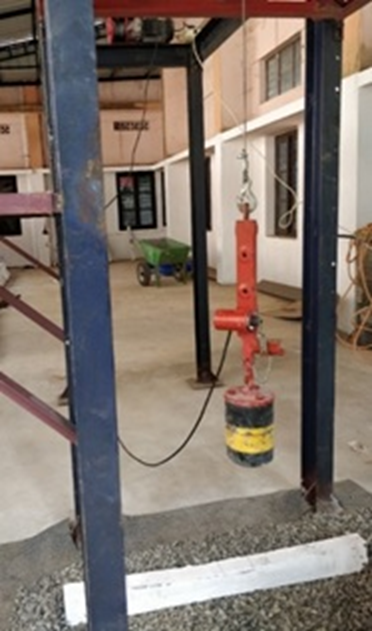
Fig.4 Impact testing of sleepers [4]
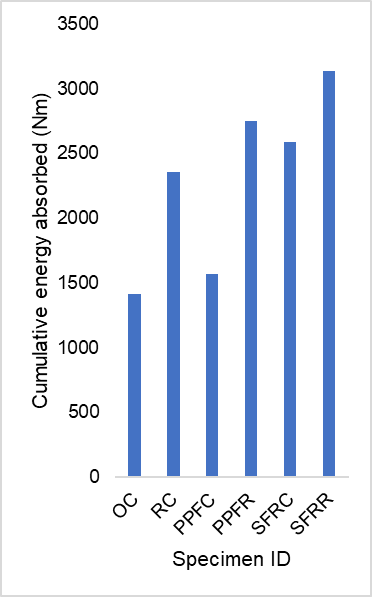
Fig.5 Results of impact tests on sleepers
Drop weight impact testing was used to determine the impact resistance of sleepers. The location of impact was 100 mm away from the sleeper centre. Multiple drops were made until cracking of sleeper at the bottom was noticed. Figs.4 and 5 depict the testing arrangement and results of impact testing of sleeper models. The impact resistance of sleeper models increased considerably with addition of rubber and fibres. Among fibre reinforced rubcrete specimens, the rigid steel fibres with their ability to bridge macro cracks exhibited an improvement of above 100 % in impact resistance when compared to the concrete sleepers. Thus, it can be noticed that using fibre reinforced rubcrete can potentially improve the impact resistance of sleepers.
Fibre-reinforced rubcrete sleepers offer a unique opportunity to address environmental concerns in two ways. Firstly, they can replace traditional concrete sleepers, leading to the conservation of approximately 14 tonnes of fine aggregates per kilometre of railway track. This not only reduces the extraction of these valuable resources but also minimizes the environmental impact associated with their mining and transportation. Secondly, these sleepers utilize 4 tonnes of crumb rubber per kilometre, effectively transforming a potential environmental hazard – discarded tires – into a valuable construction material. This innovative approach not only promotes resource efficiency but also contributes to responsible waste management, making fibre-reinforced rubcrete sleepers a promising solution for sustainable railway infrastructure development.
References
1. Kaewunruen S, Remennikov AM (2008) Effect of a large asymmetrical wheel burden on flexural response and failure of railway concrete sleepers in track systems. Eng Fail Anal 15:1065–1075. https://doi.org/10.1016/j.engfailanal.2007.11.013
2. Silva ÉA, Pokropski D, You R, Kaewunruen S (2017) Comparison of structural design methods for railway composites and plastic sleepers and bearers. Australian Journal of Structural Engineering 7982:1–17. https://doi.org/10.1080/13287982.2017.1382045
3. Research Designs and Standards Organisations (2011) Indian railway standard specification for pre-tensioned prestressed concrete sleepers for broad gauge and metre gauge(T-39-85).
4. Raj A, Nagarajan P, Shashikala AP (2020) INVESTIGATIONS ON FIBER REINFORCED RUBCRETE FOR RAILWAY SLEEPERS. ACI Struct J 117:109–120